Difficult-to-cut Materials: Types and Machining Techniques Explained
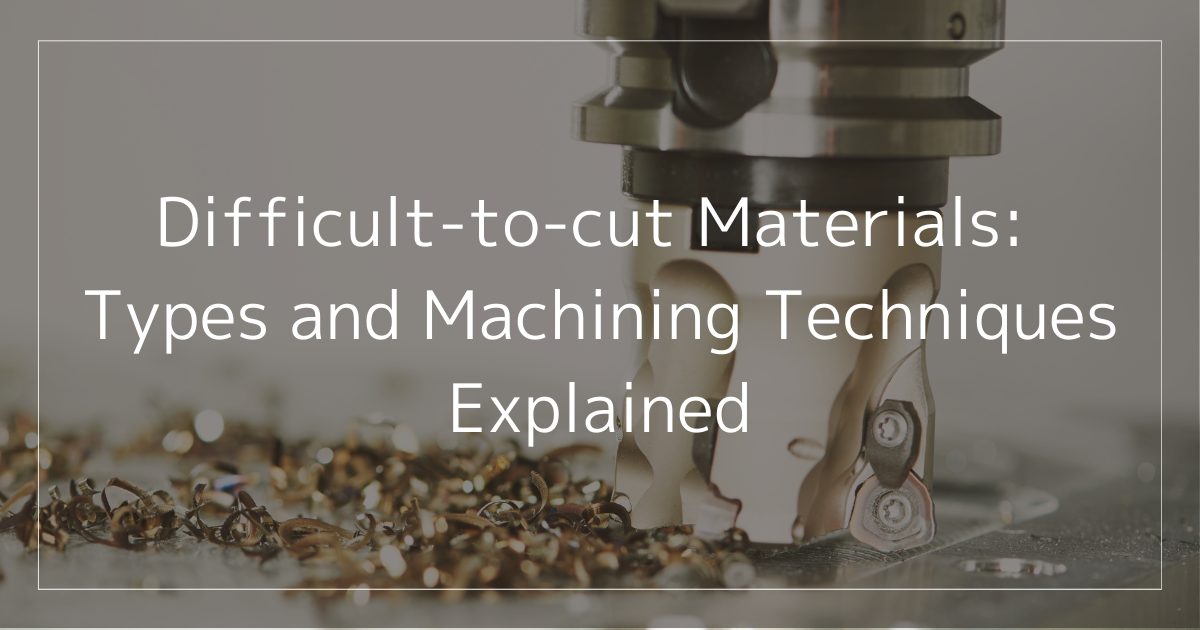
As modern industrial technology evolves, materials that are challenging to process, often referred to as ‘difficult-to-machine’ or ‘hard-to-cut materials,’ have become essential not only for cutting-edge industries but also in our everyday lives.
Machining these materials, however, demands specialized techniques and expertise that go beyond standard machining practices. This article explores the fundamental characteristics of difficult-to-machine materials, their various types, and the critical considerations for processing them.
If your company is exploring the use of these advanced materials, we hope this information proves helpful and insightful.
What are Difficult-to-Machine Materials?
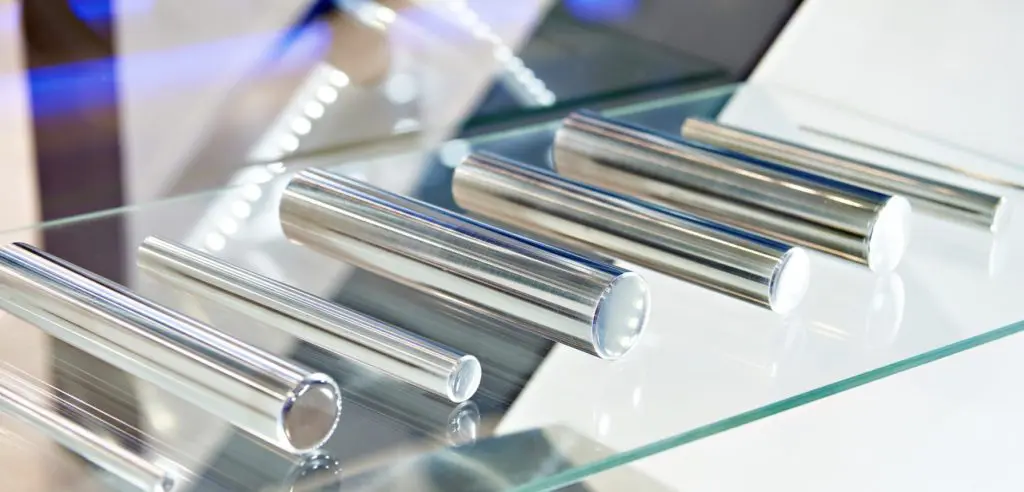
Difficult-to-machine materials are those with unique physical properties that make them challenging to machine using standard methods.
These materials demand specialized techniques, equipment, and tools to accommodate their distinctive attributes.The ability to process these materials is vital in various industries.
For example, in aerospace, they are essential for manufacturing engine components and structural parts, thanks to their heat resistance and exceptional strength.
In the medical field, these materials are ideal for implants and surgical tools due to their biocompatibility and corrosion resistance. Similarly, in electronics, they play a key role in meeting requirements for heat resistance and conductivity.
Conditions and Characteristics of Difficult-to-Machine Materials
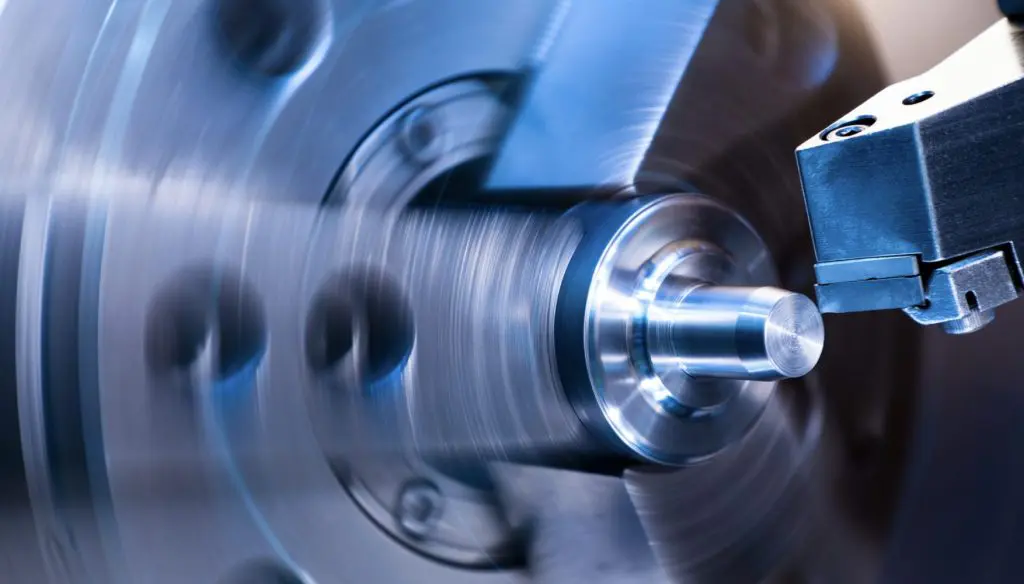
Difficult-to-machine materials typically exhibit specific characteristics that require careful attention during machining. These properties often necessitate specialized tools, techniques, and parameters:
Hardness
High hardness enhances durability and wear resistance but presents significant challenges in machining. These materials cannot be easily processed with standard tools, requiring special high-hardness tools and advanced machining methods.
Softness
Some difficult-to-machine materials are soft and prone to deformation during machining, making precise dimensional control more difficult. This is especially critical when working with thin parts or complex shapes, where small forces need to be carefully managed.
Work Hardening
Certain materials harden during machining due to heat and stress. This process, known as work hardening, increases material hardness during cutting, making machining progressively harder. It is especially noticeable during cutting and grinding, requiring optimized machining parameters to manage.
Toughness
Some materials exhibit toughness, causing them to adhere to cutting edges during machining. This behavior, stemming from their chemical or thermal properties, reduces cutting precision and accelerates tool wear. Special cooling techniques and advanced tool coatings are necessary to address these issues.
Chip Elongation
Certain materials produce long, continuous chips during cutting, which can interfere with machining processes. Effective chip control mechanisms and optimized cutting conditions are essential to maintain precision and prevent tool damage.
Brittleness
Brittle materials are prone to cracking under machining stress. This behavior is particularly challenging in methods involving impact or high pressure. Carefully controlled forces and slower processing speeds are needed to avoid material damage.
Tendency to Tear
Some materials tear instead of cutting cleanly, leading to irregularities on the surface. This makes it difficult to achieve the desired surface finish and requires precise tool adjustments to minimize defects.
Chip Welding
The high heat generated during machining can cause chips to fuse onto cutting tools, leading to wear, damage, and reduced machining quality. This issue is particularly common in high-speed or heavy cutting and can be mitigated through appropriate cooling systems and optimized cutting parameters.
Types of Typical Difficult-to-Machine Materials
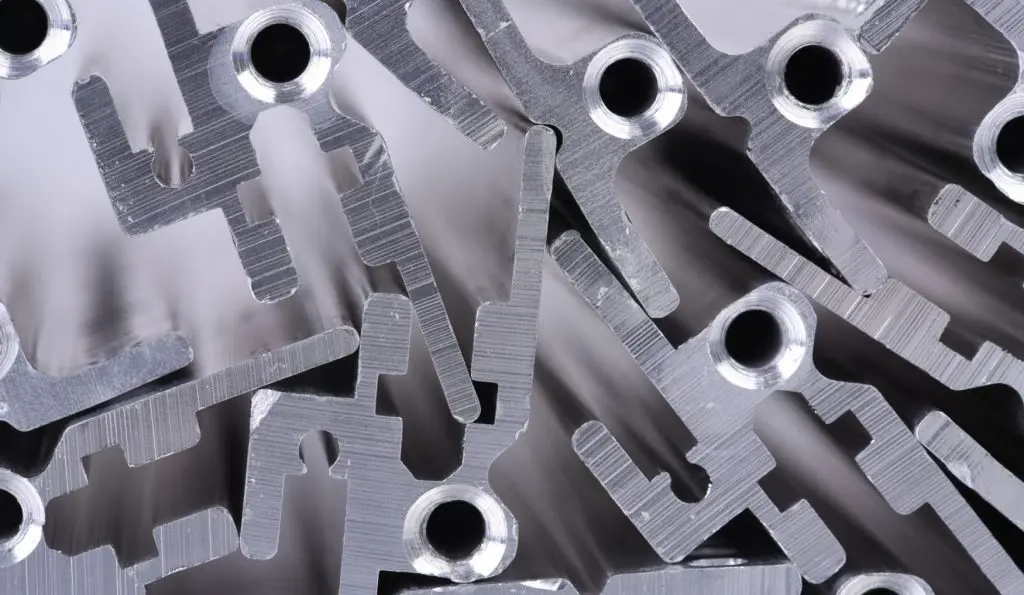
Difficult-to-machine materials are used in a wide range of industries, often because of their challenging machinability and their ability to perform under demanding conditions. These materials come in many types, each offering unique properties that make them essential in specific applications. In this section, we’ll introduce some of the most common difficult-to-machine materials and explain why they are valued in various industrial fields.
High Melting Point Materials
High melting point materials, as the name suggests, have extremely high melting points, allowing them to retain their strength and stability even under intense heat. These materials play an essential role in advanced industries where high-temperature performance is critical. They are commonly used in fields like aerospace, military technology, nuclear energy, and advanced electronics, where components need to withstand extreme conditions without compromising their functionality.
Tungsten
Tungsten is well known for its incredibly high melting point and exceptional hardness, which makes it ideal for applications where heat resistance and wear resistance are paramount. It is widely used in light bulb filaments, electronic device electrodes, and other high-performance applications that require materials capable of enduring harsh environments.
Molybdenum
Molybdenum, similar to tungsten in its properties, offers improved machinability while still maintaining excellent heat resistance and strength. This material is especially valuable in industries like aerospace and military technology, where components must endure high temperatures without failing. Its ability to withstand extreme conditions makes it a key material for applications such as aircraft parts and missiles.
Tantalum
Tantalum is known for its remarkable corrosion resistance, which makes it ideal for use in chemical reactors and medical implants. Its ability to resist corrosion even in harsh chemical environments is highly valued in industries where reliability and durability are essential. Tantalum is often used in highly specialized medical devices and implants, where biocompatibility is a must.
Niobium
Niobium is another highly specialized material, valued for its superconducting properties at low temperatures. This makes it an important material in scientific research, particularly in applications such as particle accelerators and other advanced technologies. Its ability to maintain superconductivity at low temperatures has made it indispensable for modern science and technology.
Pure Metals
While many metals are commonly alloyed to enhance their strength or other properties, pure metals are often chosen for specific applications where their natural properties are needed. These materials are used in industries that require the highest level of purity, conductivity, or other specialized characteristics. Examples of pure metals include gold, silver, and copper, each of which has unique properties that make it suitable for specialized uses in electronics, medical devices, and other fields where quality and performance cannot be compromised.
Nickel Alloys
Nickel alloys are highly valued for their ability to perform in extremely demanding environments. These materials stand out due to their outstanding heat resistance, corrosion resistance, and high mechanical strength, making them ideal for use in situations where other materials might fail. By adding elements such as chromium, iron, and molybdenum to the base of nickel, these alloys significantly enhance performance in specific conditions. As a result, nickel alloys are widely used in industries such as aerospace, chemical processing, and more.
For example, they are commonly found in jet engine components within the aerospace industry and as materials in reactors that must endure highly corrosive environments in the chemical sector.
Inconel
Inconel alloys are known for their exceptional strength and oxidation resistance, particularly in high-temperature environments. This makes them ideal for use in jet engines, gas turbines, and chemical plants, where both heat and corrosion resistance are critical.
Hastelloy
Hastelloy is particularly renowned for its corrosion resistance, which makes it indispensable in industries like chemical processing and marine environments, where exposure to aggressive chemicals and harsh conditions is common. Its high resistance to both oxidation and corrosion allows it to perform reliably in these demanding applications.
For more details on Hastelloy, please refer to [relevant resources].
Super Invar
Super Invar is characterized by its extremely low thermal expansion rate, which is highly beneficial for applications that require precision. It is commonly used in precision instruments, electronic devices, and other specialized applications where dimensional stability is crucial, even under varying temperatures.
Permalloy
Permalloy is a nickel-iron alloy known for its high magnetic permeability, making it essential in the design and construction of magnetic sensors and transformers. Its ability to enhance magnetic fields is a key reason it is used in a variety of electronic devices.
Additionally, Permendur, a cobalt-based alloy, is another material that can be used to control magnetism through heat treatment. It is often found in recording media and magnetic switches, where its magnetic properties play a vital role in their function.
Precious Metals
Precious metals have been valued for their rarity and beauty throughout history, and today they are crucial in advanced industries due to their unique properties. Pure silver and platinum are known for their excellent conductivity, corrosion resistance, and chemical stability, making them vital in areas such as electronic components, catalysts, and precision instruments.
Pure Silver
With high conductivity and reflectivity, pure silver is used in electrical contacts and mirror manufacturing.
Platinum
Platinum’s chemical stability makes it ideal for catalysts and jewelry applications.
Brittle Materials
Brittle materials are those that, while hard and heat-resistant, are prone to break or crack under pressure or impact.
Ceramics
With high hardness and heat resistance, ceramics are commonly used in engine components and cutting tools.
Quartz Glass
Known for its high purity, quartz glass is crucial in optical instruments and semiconductor manufacturing.
Quartz Crystal
Quartz crystals are valued for their ability to maintain accurate frequencies, making them essential in clocks and communication devices.
Efficient Machining Conditions for Difficult-to-Machine Materials
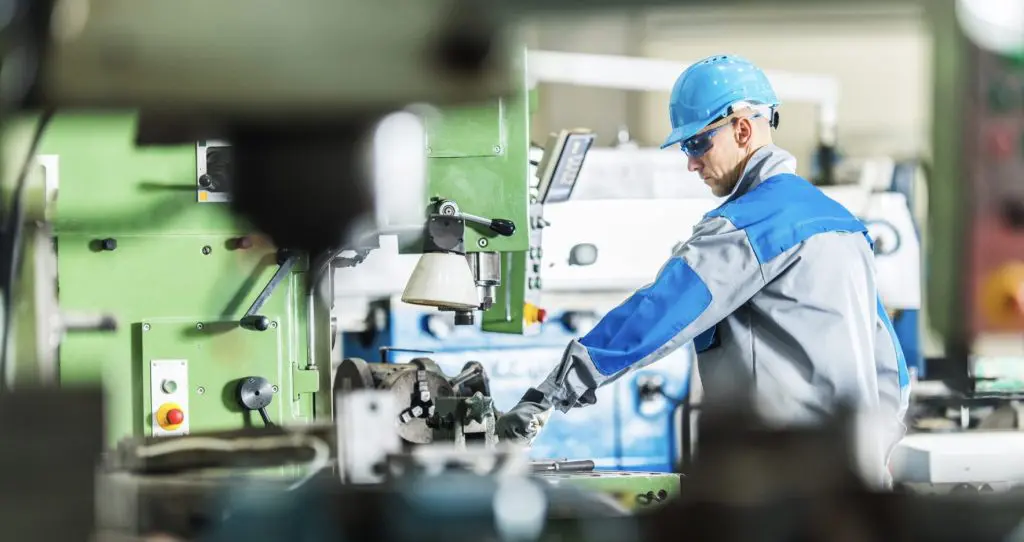
When machining difficult-to-machine materials, it’s essential to adjust your approach to match their unique characteristics. Here are some key conditions to improve efficiency:
Appropriate Tool Selection
Choosing the right tools is critical. Tools with high hardness and heat resistance, such as cemented carbide, ceramic, and diamond-coated tools, are ideal for handling the extreme hardness and wear resistance of these materials. Selecting the proper tools not only boosts efficiency but also improves machining precision and extends tool life.
Low-Speed, High-Torque Machining
For these materials, low-speed, high-torque machining is recommended. This approach helps prevent material damage and reduces excessive heat. It allows better control over cutting resistance and helps minimize internal stresses in the material.
Use of Coolants
Machining generates heat, which can cause tool wear and material degradation. Using coolants effectively can reduce these problems by lowering temperatures at the cutting zone, aiding in chip removal, and minimizing friction between the tool and material.
Micro-Machining Techniques
Precision is especially important when working with difficult-to-machine materials. Micro-machining techniques, such as micro-cutting tools, advanced NC technology, and laser machining, help achieve the high level of dimensional control required.
Regular Tool Replacement
Tools wear out faster when machining difficult materials, so frequent replacement is necessary to maintain efficiency. Regular tool inspection and maintenance are crucial to ensuring optimal performance, accuracy, and reducing downtime.
Trust Koyo High Precision for Machining Difficult-to-Cut Materials
At Koyo High Precision, we combine cutting-edge technology with years of hands-on experience to expertly handle the machining of even the most difficult-to-cut materials.
No matter how challenging the material, we can identify the perfect machining conditions by carefully monitoring chip formation, tool wear, cutting surface quality, and even the sounds during machining.
We are committed to providing customized solutions that meet your unique needs. Contact us today for consultations or quotations — we’re here to help with all your difficult-to-machine material requirements.