Hastelloy Machining: Key Points | Material Properties, Types, and Applications
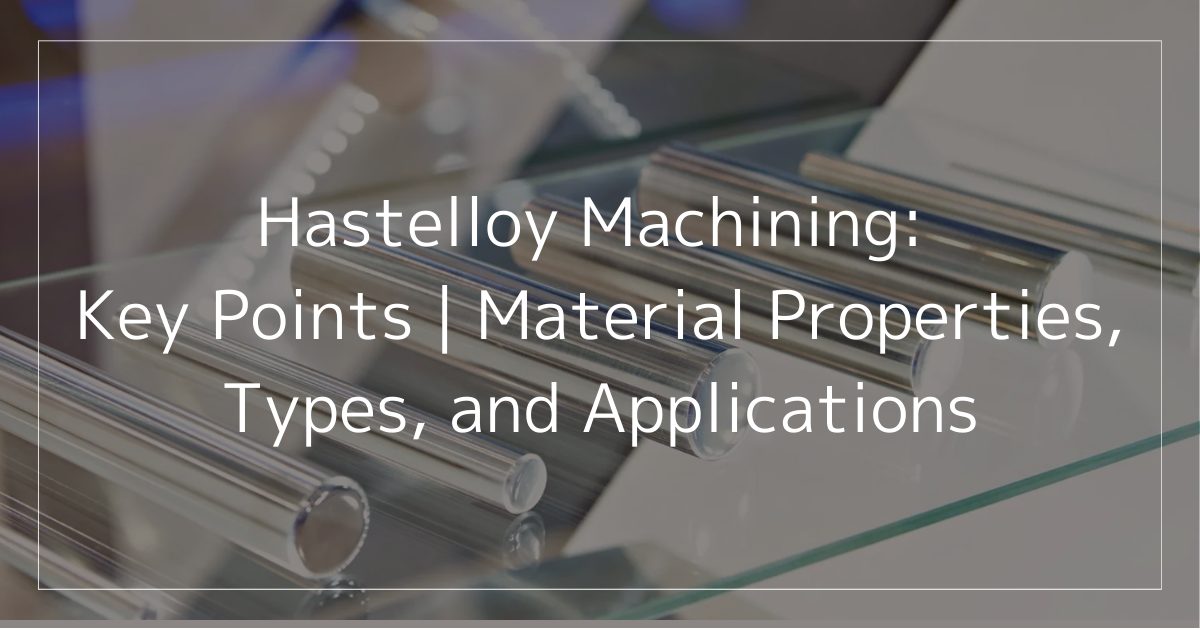
Hastelloy is a unique nickel-based alloy that maintains its performance even in harsh environments due to its exceptional corrosion resistance and heat resistance.
This article will explain in detail the various applications of Hastelloy, its distinct physical properties, challenges in machining, and its types and characteristics. If your company is considering material processing using Hastelloy, please use this as a reference.
What’s Hastelloy?
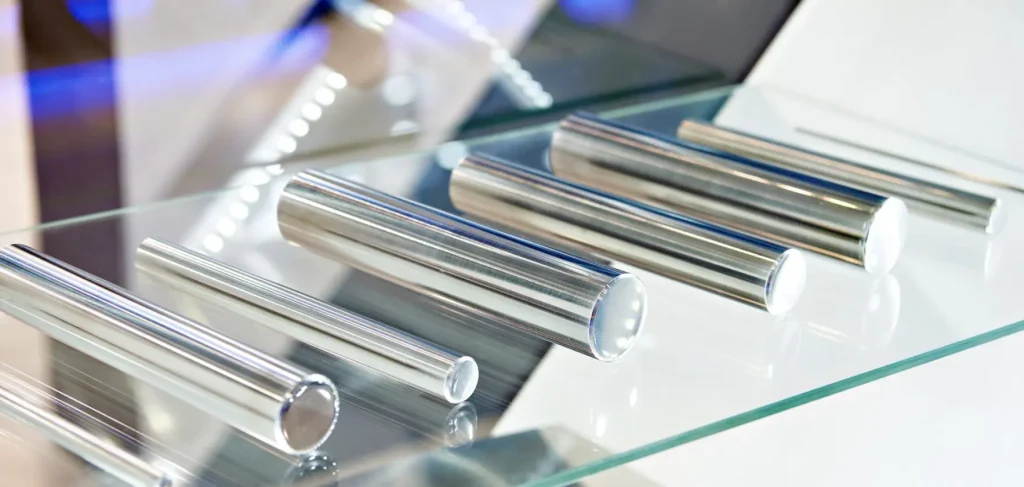
Hastelloy is a unique nickel-based alloy that maintains its performance even in harsh environments due to its exceptional corrosion resistance and heat resistance.
This article will explain in detail the various applications of Hastelloy, its distinct physical properties, challenges in machining, and its types and characteristics. If your company is considering material processing using Hastelloy, please use this as a reference.
Hastelloy is a heat-resistant alloy with nickel as its main component, known for its excellent corrosion and heat resistance.
It is used in a wide range of fields, including the chemical industry, as it maintains its performance even under extreme conditions.
In the chemical industry, where highly corrosive liquids and gases are constantly present, Hastelloy is used in components such as pipelines, valves, pumps, and reactors that require corrosion resistance.
The excellent corrosion resistance of Hastelloy protects these components from corrosion damage, enabling stable plant operation and extended service life.
Characteristics of Hastelloy
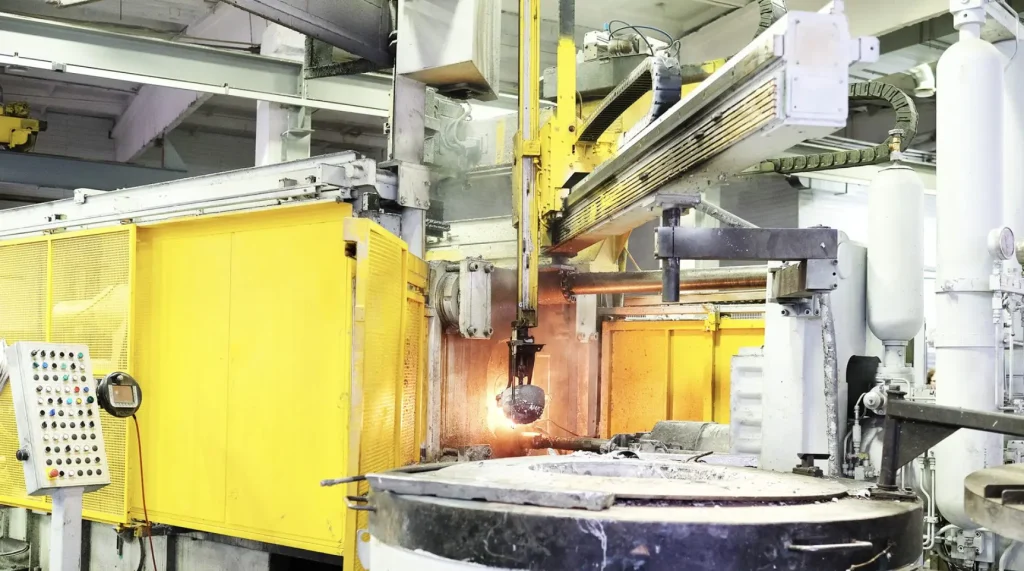
Hastelloy is valued in various fields for the following characteristics:
High Corrosion Resistance
Hastelloy offers unmatched resistance to various corrosive substances, such as strong acids and salts, providing high chemical stability with minimal degradation or damage from corrosion.
In chemical plants, where strong acids and bases are commonly used, high-corrosion-resistant materials like Hastelloy are crucial to ensure the safety and durability of equipment, even in these harsh environments.
As a result, Hastelloy is widely used in applications that require corrosion-resistant materials, such as pipes, heat exchangers, and reactor linings.
Excellent Heat Resistance
Another feature of Hastelloy is its ability to maintain its strength and corrosion resistance without compromising its performance, even in high-temperature environments.
This heat resistance is highly valued in applications where stable performance at high temperatures is required, such as jet engine and gas turbine parts in the aerospace industry, industrial furnaces, and heat treatment equipment.
Heat resistance allows for stable operation over long periods by suppressing material degradation, contributing to lower maintenance costs.
High-Performance Material Surpassing Titanium
While titanium is also known as a material with excellent corrosion and heat resistance, Hastelloy outperforms it in performance.
It can maintain its performance even under extreme conditions, such as drastic temperature changes, high pressure, and chemically aggressive environments.
Hastelloy can be used in applications that titanium cannot, enabling its use in a wider range of industrial fields.
Types of Hastelloy
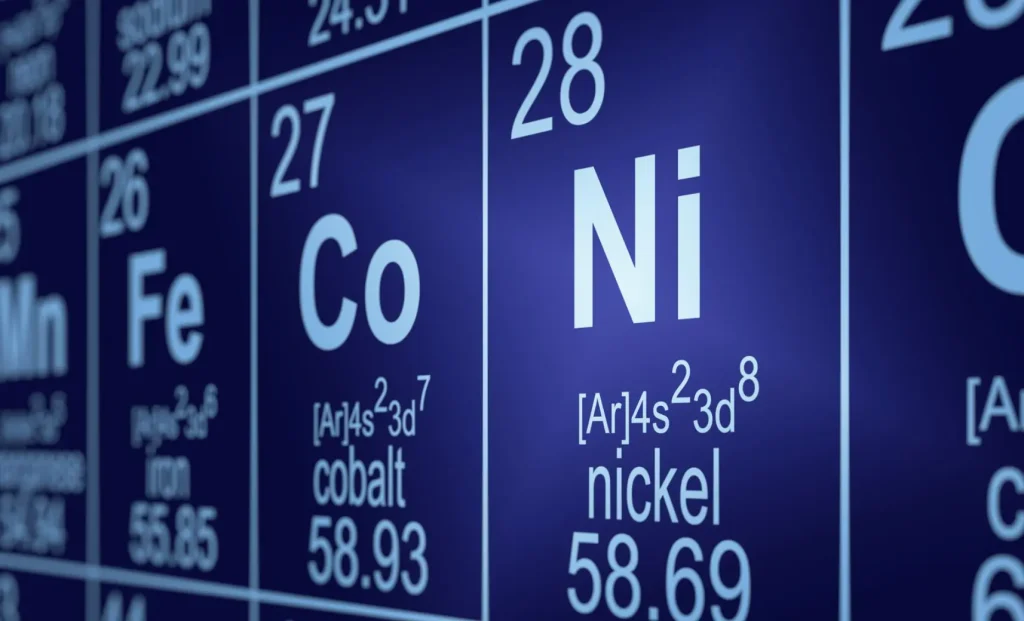
Each type of Hastelloy is optimized for specific chemical and physical conditions and designed to withstand use in harsh environments.
Here are the typical types of Hastelloy and their characteristics:
Hastelloy B-2
Hastelloy B-2 has excellent resistance to strong acids such as sulfuric and hydrochloric acids.
This resistance is very important in the chemical process industry, and it is widely used as a material for pipelines and reactors in environments where acid corrosion is a concern.
Hastelloy B-2 also maintains its corrosion resistance at high temperatures, making it a preferred material for equipment such as heat exchangers and evaporators.
Hastelloy C-22
Hastelloy C-22 demonstrates outstanding corrosion resistance to a wide range of chemicals and has exceptional resistance to oxidizers in particular.
Because of this, it is highly valued in chemical plants and wastewater treatment facilities where strong oxidizers, such as chlorine and hydrogen peroxide, are used.
Its remarkable heat resistance also ensures long-term reliability in processes where high-temperature corrosion is a critical concern.
Hastelloy C-276
Hastelloy C-276 exhibits exceptional corrosion resistance to various sources of corrosion such as seawater, chlorides, oxidizers, and reducing agents.
Due to this versatility, it is widely adopted in a broad range of fields, including the chemical industry, oil and gas industry, and environmental technology.
It particularly shows its true value in environments where both corrosion and wear occur simultaneously, significantly extending the service life of equipment.
Hastelloy X
Hastelloy X has excellent resistance to high-temperature strength, oxidation, and carbide precipitation.
Therefore, it is particularly valued in the aerospace industry and is used as a material for jet engine thermal components and gas turbine components.
Its heat resistance also makes it suitable as a material for equipment used in high-temperature environments such as industrial furnaces, providing stable performance over a long period.
Hastelloy is Classified as a “Difficult-to-Cut Material”
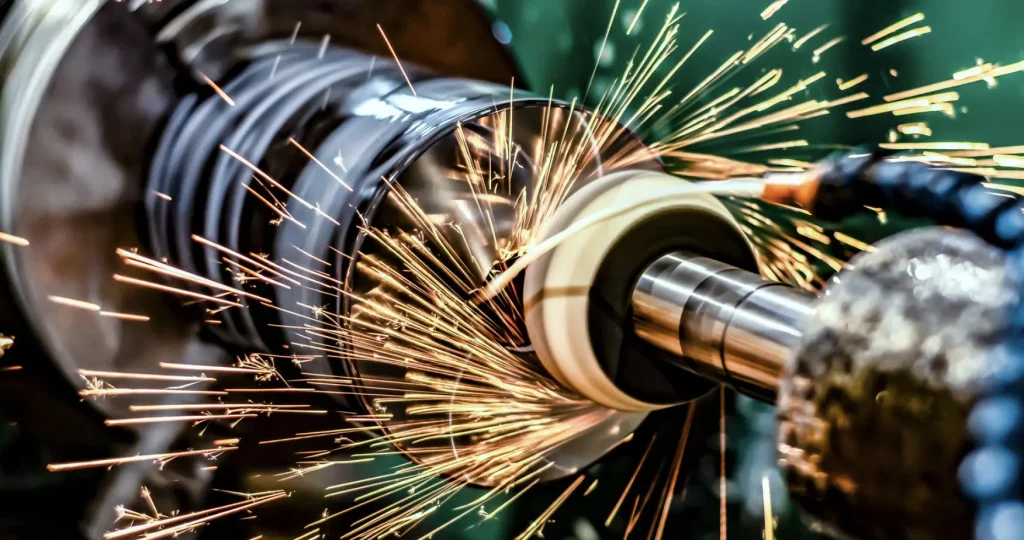
Due to its excellent properties mentioned above, Hastelloy is also known as a “difficult-to-cut material” and is recognized for its difficulty in machining.
Low Thermal Conductivity
The low thermal conductivity of Hastelloy causes specific problems during machining.
Specifically, the heat generated during machining does not transfer to the material side but concentrates on the tool side, causing the tool to become overheated. This high temperature leads to significant wear on the cutting edge.
To prevent this, it is effective to carefully manage machining speed and feed rate, choose tool materials that can withstand high temperatures, and use high-pressure coolant to forcibly remove heat from the cutting edge.
Work Hardening
Another characteristic of Hastelloy is that it tends to harden during machining.
This hardening occurs when great pressure is applied to the material surface during machining, causing the material to deform. Work hardening further increases the hardness of the material after machining, increasing resistance to cutting tools and promoting tool wear.
Work hardening can also make finishing work in subsequent processes difficult, requiring skilled techniques and advanced machining strategies to achieve high-precision machining.
High Hardness
High-hardness materials are highly resistant to cutting tools, which can lead to faster tool wear.
In addition, achieving precise dimensions and a smooth finish requires machines with high precision and operators with extensive experience and expertise.
Because of these factors, special tool materials, such as cemented carbides and ceramics, are often recommended for machining Hastelloy, which can drive up machining costs.
Key points in Hastelloy processing
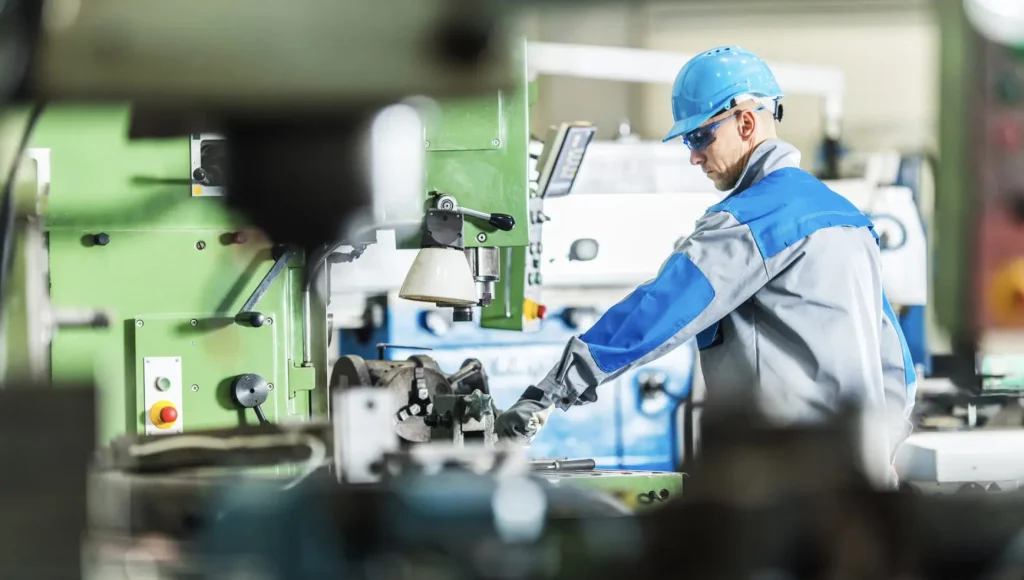
Machining Hastelloy requires precise machining technology adapted to its unique physical properties and appropriate tool selection.
Use Appropriate Drills
To cope with the hardness and heat resistance of Hastelloy, selecting specialized tools is essential.
Drills made of heat-resistant cemented carbide or ceramics can not only withstand the hardness of Hastelloy but also maintain their cutting performance at high temperatures.
These tools are specifically designed to counteract the material’s hardness and provide excellent durability, even with long-term use.
However, these special tools are more expensive than regular ones, so careful planning and preparation before use are important.
Pay Attention to Drill Rotation Speed
The drill’s rotation speed directly impacts both the efficiency and precision of machining.
For Hastelloy, high rotation speeds generate excessive heat, which can damage the material or tool.
That’s why it’s important to find the optimal rotation speed. It’s typically recommended to use a lower speed and closely monitor the cutting progress.
Regularly checking the machining process and adjusting the rotation speed or replacing tools when needed is key to achieving high-quality results.
Use Plenty of Cutting Oil
The use of cutting oil, like coolants, is crucial in Hastelloy machining.
Cutting oils help reduce friction between the tool and material while dissipating the heat generated during machining. By using the right amount of cutting oil, tool wear can be minimized, and uneven heating of the material can be avoided.
Especially when machining materials with low thermal conductivity like Hastelloy, using an adequate amount of cutting oil like coolants can extend the life of both the tool and the material.
Trust Koyo High Precision for Machining Difficult-to-Cut Materials
At Koyo High Precision, we combine cutting-edge technology with years of hands-on experience to expertly handle the machining of even the most difficult-to-cut materials.
No matter how challenging the material, we can identify the perfect machining conditions by carefully monitoring chip formation, tool wear, cutting surface quality, and even the sounds during machining.
We are committed to providing customized solutions that meet your unique needs. Contact us today for consultations or quotations — we’re here to help with all your difficult-to-machine material requirements.