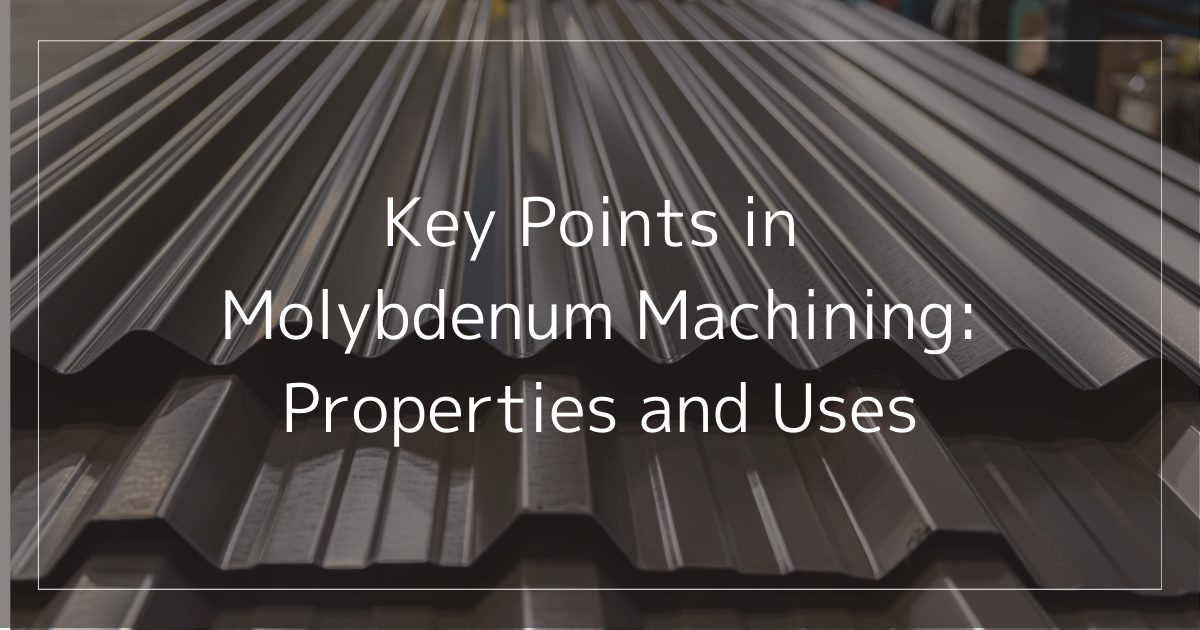
This time, we will focus on the unique properties of molybdenum, a metal well-known for its high melting point, exceptional hardness, and durability. We will also discuss its various applications across industries and the specific challenges involved in machining it.
Machining molybdenum, an essential material in many fields, requires specialized techniques and careful attention to detail due to its unique characteristics.
We encourage companies interested in using molybdenum in their processes to use this information as a helpful guide and reference.
Molybdenum
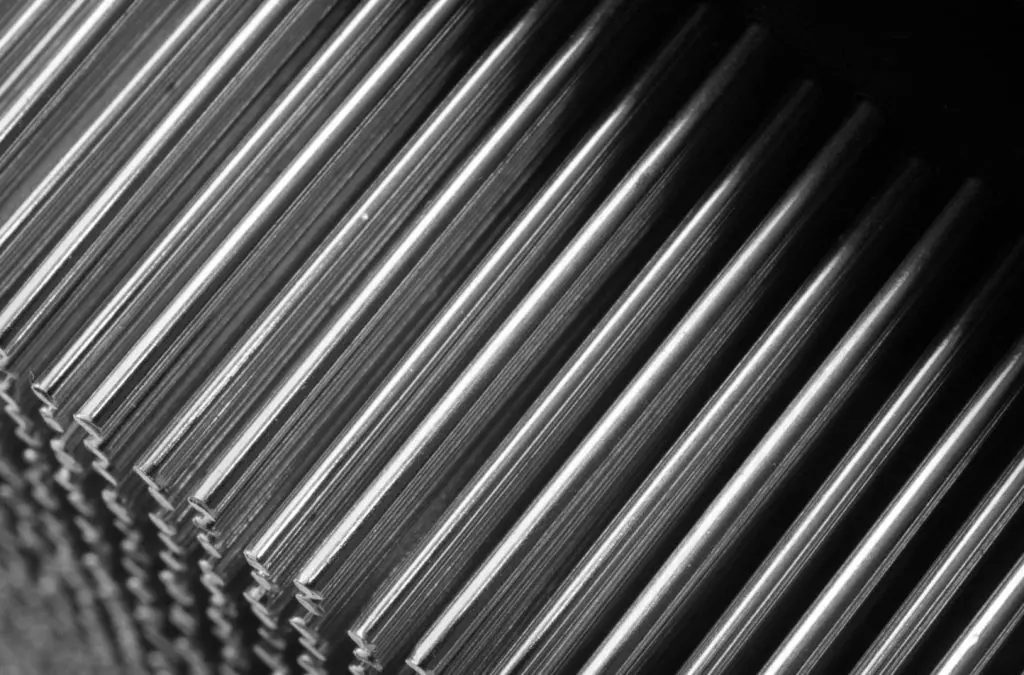
Molybdenum, represented by the symbol Mo, is a metallic element and a type of rare metal known for its high hardness and ability to withstand extremely high temperatures. It is also an essential trace element for the human body, helping with uric acid production, blood formation, and nitrogen processing, and it plays an important role in certain enzymes.
This metal is found throughout the Earth’s crust and is extracted from ores like molybdenite (molybdenum sulfide). In industry, molybdenum is used in a variety of fields, such as the steel industry, electronic components, and the aerospace sector.
Molybdenum Properties
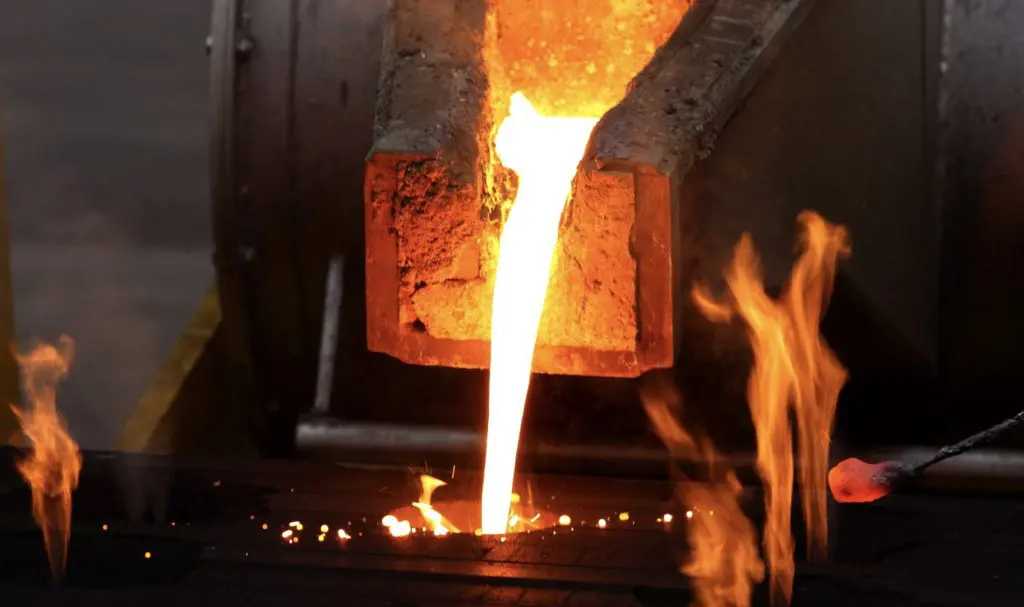
This section highlights the properties of molybdenum, divided into its physical and chemical characteristics.
Physical Properties
High Melting Point
Molybdenum has an exceptionally high melting point of 2623°C, which is far higher than that of iron (about 1538°C).
This makes it an excellent choice for use in extreme high-temperature environments, such as aerospace engineering and high-temperature furnaces, where durability under heat is critical.
High Strength
Molybdenum is not only strong at room temperature but also retains its strength even at high temperatures.
This property makes it ideal for demanding applications, such as aircraft engines and industrial furnaces, where materials are exposed to extreme heat. Unlike many metals that weaken at higher temperatures, molybdenum maintains its strength with only minimal reduction, ensuring reliability and stability during use in high-temperature conditions.
Chemical Properties
Corrosion Resistance
Molybdenum is highly resistant to corrosion caused by many acids and alkalis.
This makes it an excellent material for equipment and components used in harsh environments, such as the chemical industry and marine applications.
Its corrosion resistance also ensures long-term durability and reliability, helping reduce maintenance costs and improving efficiency over time.
Reactivity
Under specific conditions, molybdenum reacts with oxygen, certain gases, and various furnace materials, making it valuable as a catalyst in chemical reactions.
For instance, it is widely used as a catalyst in petroleum refining and chemical synthesis, as well as in facilitating specific reactions in industrial processes.
These physical and chemical properties highlight the vital role of molybdenum in modern industrial technology. Its ability to withstand extreme environments, high temperatures, and corrosive conditions makes it indispensable for industries requiring durable and reliable materials.
Molybdenum’s strength and heat resistance make it ideal for applications in high-temperature environments, while its corrosion resistance is perfect for use in the chemical industry and marine sectors. Additionally, its role as a catalyst expands its applications across various chemical processes, showcasing its versatility in modern manufacturing.
Applications of Molybdenum
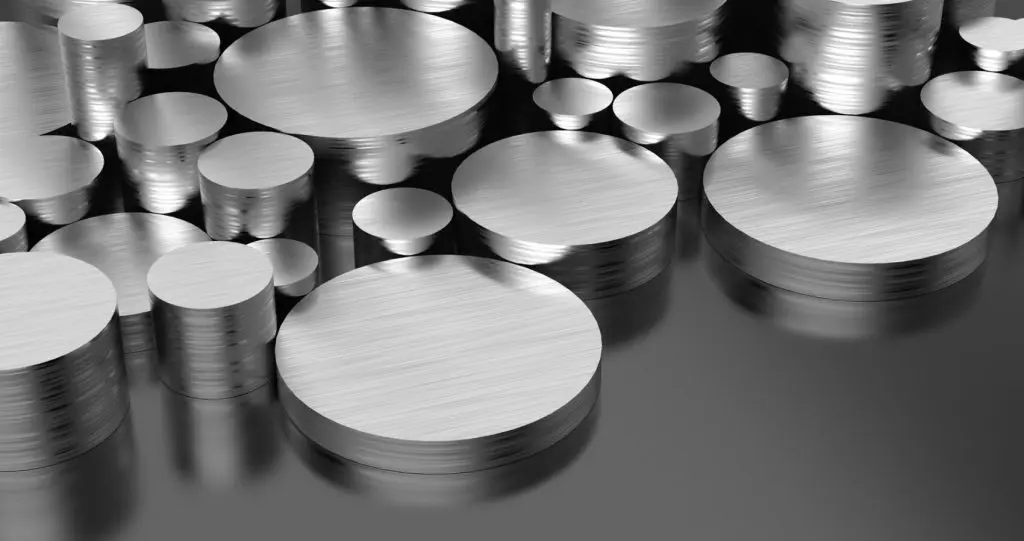
Thanks to its unique properties, molybdenum is used in a wide variety of industries and applications.
Heating Elements, Reflectors, and Structural Components in High-Temperature Electric Furnaces
Molybdenum’s high melting point and excellent heat resistance make it ideal for components in high-temperature electric furnaces. When used as heating elements, reflectors, or structural parts, it retains its strength and delivers stable performance even under prolonged high-temperature conditions.
Sintering Trays for Ceramics and Magnetic Materials
Molybdenum is widely used in heat treatment processes. Its ability to withstand high temperatures and provide uniform heating makes it an excellent material for sintering trays used in ceramics and magnetic material production.
Gate Formation in Integrated Circuits and Heat Dissipation Substrates for Semiconductors
With its high electrical conductivity, molybdenum plays a crucial role in forming gates for integrated circuits and as a heat dissipation substrate material for semiconductors. These applications improve the performance and reliability of electronic devices.
Components in Microwave Ovens and Filament Supports in Light Bulbs
Molybdenum is used in components that require both heat resistance and strength. It is especially valuable in microwave ovens and as filament supports in incandescent light bulbs.
Additive Material in Steel Production (High-Speed Steel, Heat-Resistant Steel, Alloy Tool Steel, etc.)
As an additive in steel production, molybdenum enhances the properties of high-speed steel, heat-resistant steel, and alloy tool steel. Its addition improves hardness, heat resistance, and wear resistance, enabling the production of tougher and more durable steel products.
Manufacturing of Mechanical Parts, Molds, and Electronic Components
Molybdenum’s properties are highly beneficial in producing mechanical parts, molds, and electronic components. Its machinability, durability, and precision make it a reliable material for applications where accuracy and long-term performance are essential.
Challenges in Molybdenum Machining and Required Countermeasures
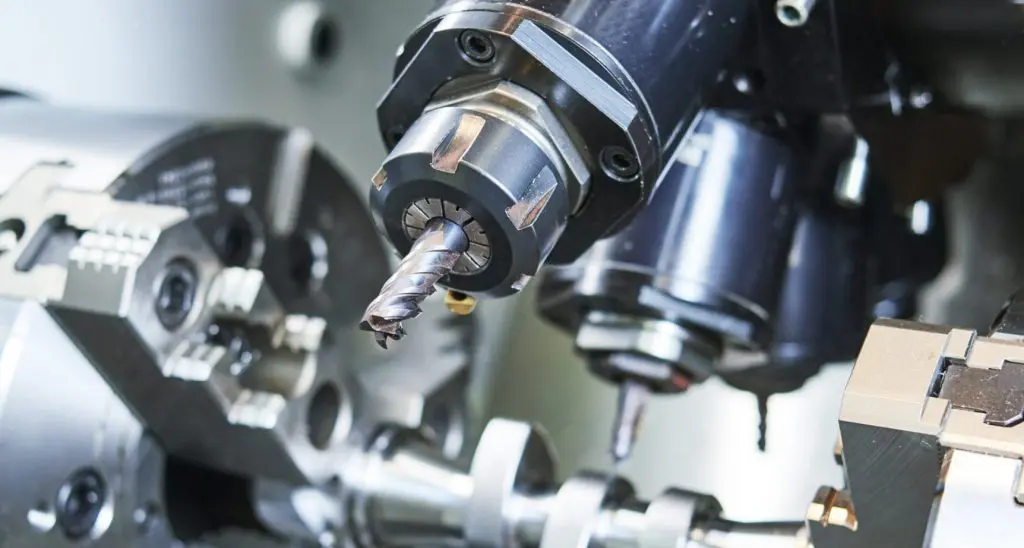
Processing molybdenum comes with unique challenges due to its physical properties. Its high hardness and brittle nature are the main factors that make machining difficult.
High Hardness
Molybdenum is an extremely hard metal, requiring special tools and techniques for machining.
Standard cutting tools wear out quickly, so ultra-hard cutters and special cutting fluids are essential. Additionally, precise control over cutting speed and feed rate is crucial to achieve accurate results when working with such hard materials.
Brittleness
Molybdenum’s brittle nature makes it prone to cracking or breaking during machining.
To prevent this, machining processes must be carefully designed to distribute the load evenly across the material. Techniques like using shallow cutting depths or dividing the process into smaller, incremental steps can reduce the risk of damage.
Temperature Management
Managing temperature is critical during molybdenum machining.
Excessive frictional heat from machining can alter the material’s properties and reduce precision. Proper cooling methods and effective temperature control must be applied to maintain machining accuracy and prevent overheating.
Minimizing Distortion
Distortion during machining is another major challenge. Residual stresses or damage from the machining process can lead to cracks or deformation during later use.
Effective countermeasures include post-machining heat treatments or adopting a gradual machining process to minimize residual stresses.
Trust Koyo High Precision for Your Molybdenum Machining Needs
Molybdenum is no ordinary material—it demands precision and expertise, and that’s where we shine.
At Koyo High Precision, we bring cutting-edge technical skills and years of hands-on experience to every project. Whether it’s a complex challenge or a tough task, we’ve got it covered.
We leverage advanced technology to work with molybdenum, using methods specially designed for its unique properties, and always meet the highest industry standards.
When it comes to machining, we don’t just meet expectations—we exceed them. Get in touch with us today for any questions or to start your next project.