Machining Techniques and Tips: A Comprehensive Guide to Cutting Processes
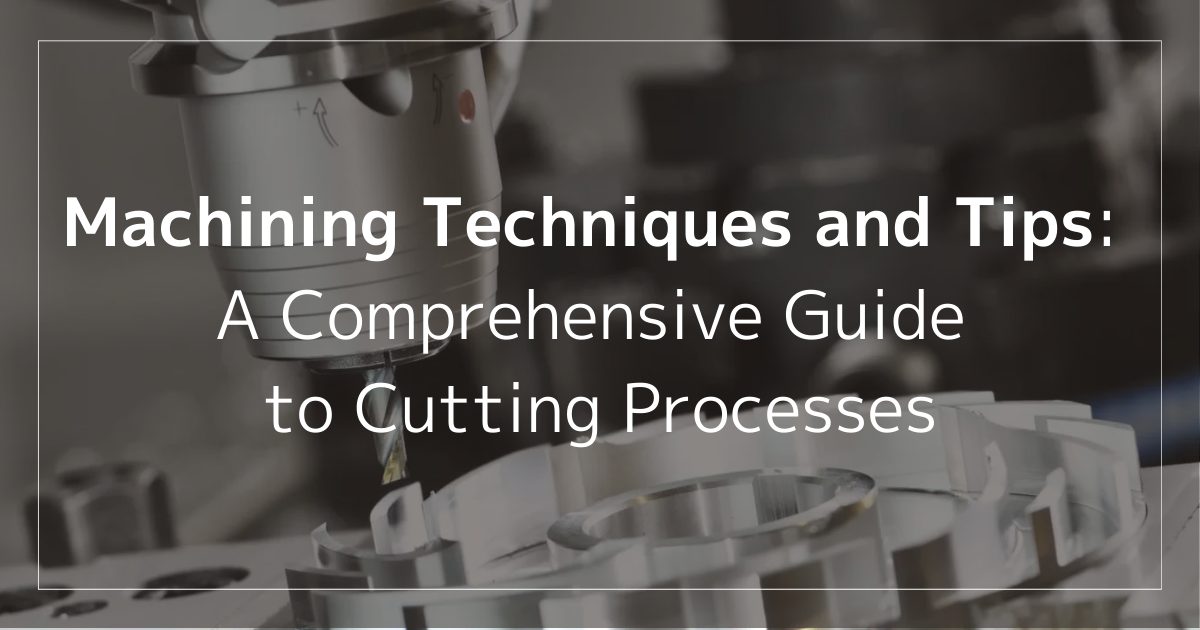
Metal Cutting Processes

Cutting processes are essential for precision parts manufacturing, allowing materials to be machined into specific shapes and sizes.
This article explores various techniques for shaping materials, from lathe machining to milling and drilling operations. Additionally, we will introduce the advantages of Computer Numerical Control (CNC) technology in achieving high precision, as well as efficient chip management methods used in cutting processes.
Cutting processing (metal cutting) is a method of removing excess material to machine workpieces into desired shapes and sizes. This process uses specific tools called cutting tools to remove material from metals, wood, plastics, and other materials. The precision and finish of the machining depend on the tool shape, material, and rotation speed.
Metal Cutting Methods
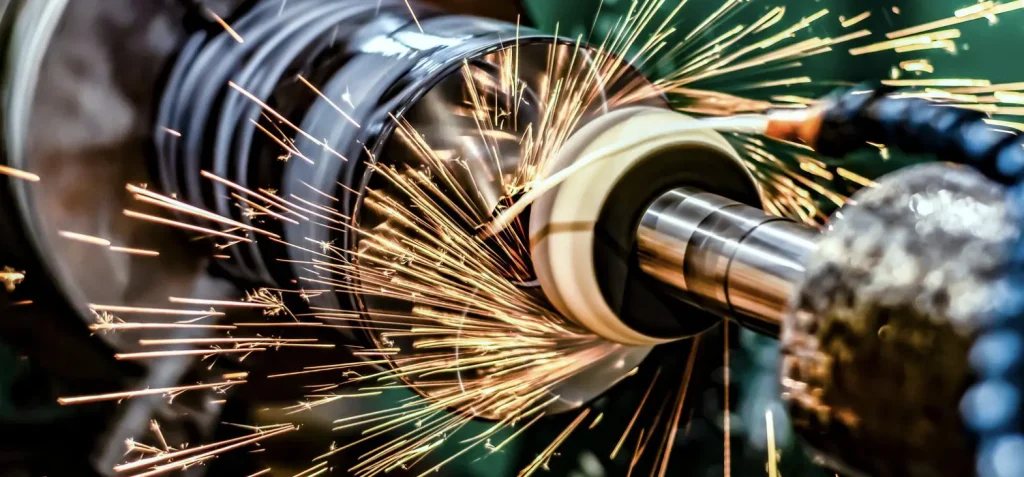
There are several metal cutting methods, and the appropriate method must be selected based on the metal’s properties and the intended application.
Lathe Machining
Lathe machining is a technique that removes material using a fixed cutting tool while rotating the workpiece. This machining method is primarily used for cylindrical parts and products requiring complex curved surfaces.
Using a lathe enables precise machining of both external and internal diameters, and it is frequently employed in manufacturing automotive engines and aircraft components.
Milling
Milling uses specialized cutting tools called milling cutters to shape planes, grooves, or gears from a workpiece.
This method is characterized by its wide range of applications, as it can create various shapes by using different cutter types and sizes. By precisely controlling the tool rotation speed, feed rate, and cutting depth, milling can achieve extremely accurate dimensions and smooth surfaces.
Drilling
Drilling is the process of creating holes in materials using drill bits. This machining technique excels in its ability to create holes of different diameters and depths with high precision.
Hole-making is a critical step in most manufacturing processes, particularly when assembling components with bolts and rivets, where precise hole positioning and sizing are required.
Drilling is widely used for machining mechanical parts as well as producing small components like electronic circuit boards.
Advantages of Cutting Processes
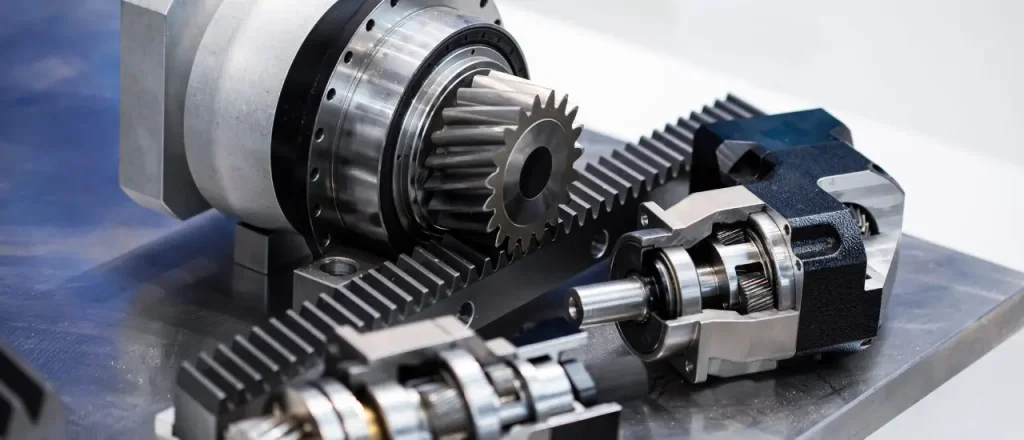
High-Precision Machining
One of the greatest advantages of cutting processes is the ability to manufacture parts with extremely high precision. This is especially true when using Computer Numerical Control (CNC) machines, which can achieve dimensional accuracy at the micron level.
High machining precision is essential for industries with strict tolerances, such as aerospace and medical device manufacturing. The ability to repeatedly produce identical parts in a highly controlled environment greatly enhances quality assurance.
Complex Shape Machining
The flexibility of cutting processes is also a major advantage. By utilizing various machines such as lathes, milling machines, and CNC routers, manufacturers can produce parts with complex 3D shapes and fine features.
It is possible to create precision-formed parts from a single solid block, reducing the need for assembly steps. For example, custom-made gears and mechanical parts with special profiles can be efficiently and accurately manufactured.
Minimal Material Deformation
In cutting processes, the force applied to the material is minimized, which helps prevent deformation during machining.
Maintaining the dimensional and shape accuracy of parts is extremely important, especially in precision manufacturing. Cutting processes can minimize internal stress in the workpiece, improving the quality and lifespan of the final product.
Disadvantages and Considerations of Cutting Processes

Time-Consuming Process
Material removal in cutting processes occurs layer by layer to achieve the desired shape. This takes time, especially when large amounts of material must be removed or when machining very complex parts.
For example, when manufacturing small precision parts from a large metal block, the more material that becomes waste, the more time is required for the removal process. Therefore, particularly for one-off items, this time consumption can be a significant barrier when project time efficiency is an important factor.
Tool Wear
In cutting processes, tools rotating at high speeds are in direct contact with materials, which increase the risk of tool wear and damage.
If the tool material or cutting speed is not properly selected, tool wear can occur at a faster rate, affecting machining accuracy and production efficiency.
Key Points in Cutting Processes
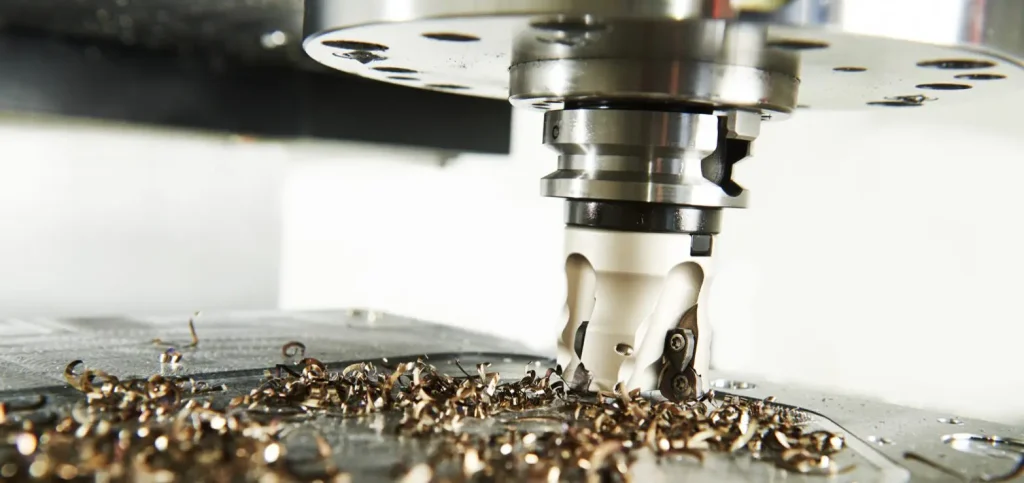
Chip Management
Chips generated during material cutting can significantly impact machining precision and reduce machine operating efficiency.
Using an effective chip removal system is essential to maintain a clean work area and reducing heat accumulation. Proper chip management helps ensure smooth machining surfaces and extends tool life. For example, using a high-pressure coolant system can rapidly evacuate chips, supporting continuous production processes.
Appropriate Tool Selection
The selection of cutting tools directly affects machining efficiency and quality. High-performance carbide tools, with their excellent wear resistance and heat resistance, enable long-term operation, reducing the frequency of tool changes and enhancing overall productivity.
Additionally, applying appropriate coatings to tools can reduce wear and boost cutting performance. For example, coatings such as titanium aluminum nitride are proven to extend tool life in high-temperature cutting operations.
Trust Koyo High Precision for Machining Materials
At Koyo High Precision, we combine cutting-edge technology with years of hands-on experience to expertly handle the machining of even the most difficult-to-cut materials.
No matter how challenging the material, we can identify the perfect machining conditions by carefully monitoring chip formation, tool wear, cutting surface quality, and even the sounds during machining.
We are committed to providing customized solutions that meet your unique needs. Contact us today for consultations or quotations — we’re here to help with all your difficult-to-machine material requirements.