Tantalum Processing: Challenges, Solutions, and Applications
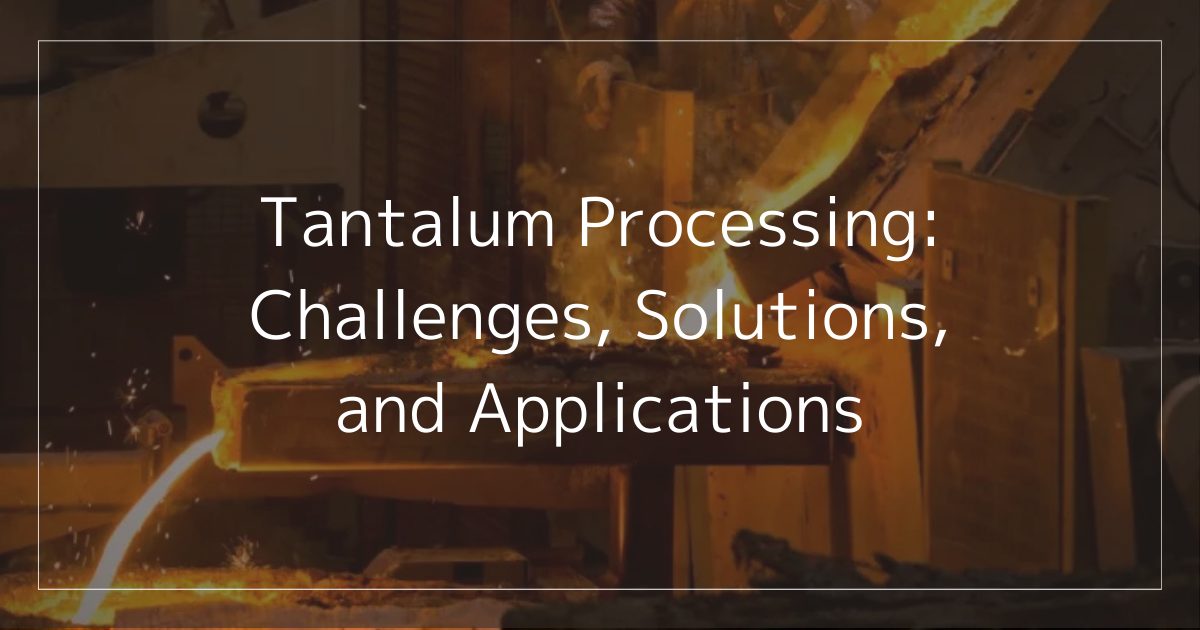
Tantalum, a rare metal known for its high corrosion resistance and melting point, is an indispensable material in modern industry. However, its excellent physical properties also make it challenging to process. This article explores the characteristics of tantalum, its applications, the major challenges in processing, and techniques to overcome them.
What is Tantalum?

Tantalum is a chemical element with the atomic number 73, belonging to Group 5 of the periodic table’s 6th period. Its chemical symbol is Ta. Known for its high corrosion resistance and high melting point, tantalum is used in various fields, including aerospace, the automotive industry, medical devices, and industrial equipment components.
Tantalum is also widely used in electronic devices, including smartphones and tablets. Moreover, due to its high thermal and electrical conductivity, it is valued in applications such as lightbulb filaments and tantalum capacitors.
Characteristics of Tantalum
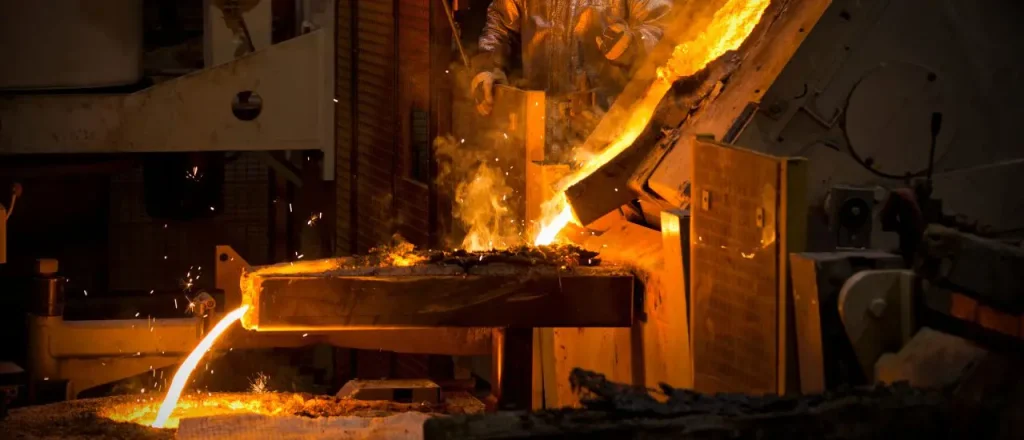
High Corrosion Resistance
One of tantalum’s most remarkable properties is its exceptional resistance to corrosion, even against strong acids. For example, tantalum remains virtually unaffected when exposed to highly corrosive substances like sulfuric acid or aqua regia. This characteristic makes it particularly valuable in the chemical industry, where materials frequently encounter harsh environments. Additionally, its corrosion resistance is highly beneficial in the medical device field, where preventing contamination is crucial.
High Melting Point
Tantalum has an extremely high melting point, allowing it to maintain material stability even in high-temperature environments. This characteristic is important in applications requiring high-temperature processing or use, such as in the manufacture of industrial furnaces or engine components that require high-temperature resistance. This property ensures that the material maintains its structural integrity over long periods of use, even under high-temperature conditions.
High Conductivity
Tantalum possesses high electrical and thermal conductivity, making it useful in electronic components and heat exchangers. Its electrical conductivity plays a crucial role in the manufacture of capacitors and high-performance semiconductor devices. Its thermal conductivity is also valuable in mechanical systems and cooling devices where essential heat transfer is necessary.
Applications of Tantalum
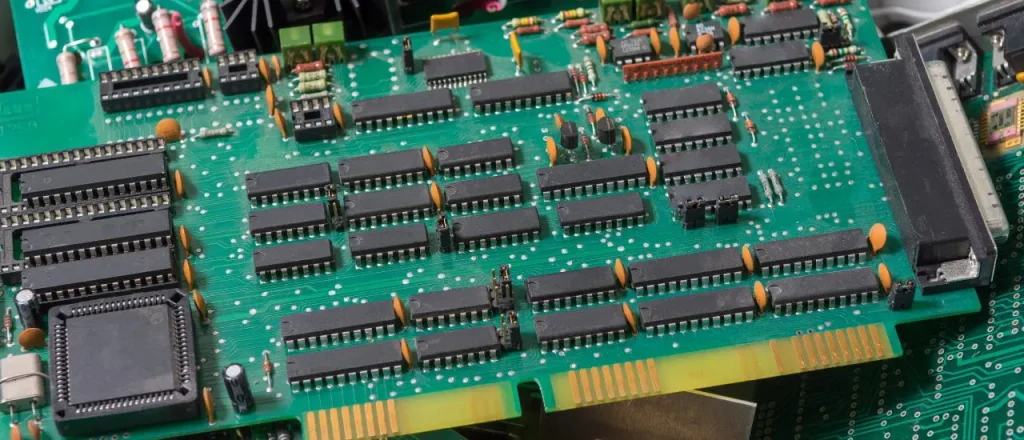
Electronics
In the field of electronics, tantalum is widely recognized as an essential material for capacitors. Tantalum capacitors, with their excellent charge storage capacity and durability, are widely used in compact electronic devices such as smartphones and computers.
Semiconductors
Tantalum also plays a crucial role in the semiconductor industry. In the manufacture of semiconductor circuit boards, tantalum acts as a barrier layer to prevent copper diffusion. This property enhances the reliability and lifespan of semiconductors, contributing to the development of more advanced electronic devices.
Aerospace Industry
In the aerospace industry, tantalum is used in the manufacture of aircraft engine turbine blades. Its high heat resistance and corrosion resistance ensure high performance even in the harsh operating environment of engines, thereby improving the safety and efficiency of aircraft.
Chemical Field
In the chemical field, tantalum is used for containers and piping used in the manufacture of pharmaceuticals and medical products. Its high resistance to corrosive substances such as strong acids and strong alkalis makes it suitable for use in environments requiring chemical stability.
The Challenges of Tantalum Processing

Tantalum has the unique characteristic of being relatively soft but hardening during processing. This work-hardening property is particularly pronounced in cutting processes, making the material difficult to cut as it becomes sticky and increasingly hard. As a result, tantalum is considered one of the most challenging materials to machine.
To minimize work hardening, it is important to select cutting tools suitable for both high-hardness and soft materials, and to implement techniques that prevent excessive hardening during processing.